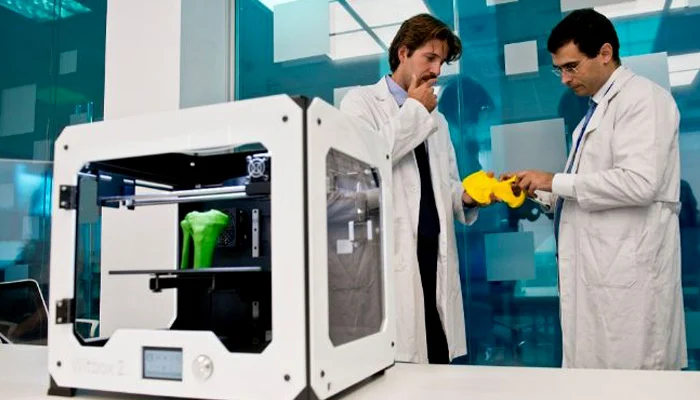
Uso de modelos de impresión 3D en Ortopedia y Traumatología: Serie de casos
- ComiteNetMD
- 2 de agosto de 2024
- Traumatología y Cirugía Ortopédica
- 0 Comments
Resumen
Introducción:
Comprender y tratar deformidades, defectos y fracturas complejas sigue siendo un desafío en el área de la Ortopedia y Traumatología. La aplicación de modelos de impresión 3D incluye el diagnóstico, la planificación quirúrgica, la creación de guías intraoperatorias e implantes y el entrenamiento quirúrgico. Las deformidades y fracturas articulares complejas representan un reto en el tratamiento quirúrgico debido a la complejidad tridimensional. La tecnología de impresión 3D permite simular la anatomía, la reducción de trazos fracturarios, osteotomías, y la dirección y longitud de los tornillos. El objetivo de este artículo es comunicar una serie de casos en los que se implementó la impresión 3D y presentar una revisión narrativa. Se describen dos casos de fractura de acetábulo, dos de escoliosis idiopática, una fractura del pilón tibial compleja y una fractura de astrágalo en los que se crearon modelos de impresión 3D para la planificación quirúrgica que resultaron beneficiosos tanto para el paciente como para el equipo quirúrgico.
Conclusiones:
Con el auge de la impresión 3D en el área de la Ortopedia y Traumatología, podremos facilitar el entendimiento de fracturas y deformidades complejas y mejorar las planificaciones prequirúrgicas. El tiempo de producción del modelo puede demorarse y ser una limitación para su uso en urgencias. Aún faltan estudios para evaluar los beneficios significativos para el paciente y el equipo médico, como la reducción del tiempo operatorio, la pérdida de sangre intraoperatoria y la exposición a la radiación.
Historia y características de la impresión 3D
El origen de la impresión 3D data de 1859 cuando François Willème desarrolla, en Francia, la primera tecnología de escaneo en 3D que denomina “foto escultura”. A partir de fotografías tomadas en 360° y con la ayuda de un pantógrafo, se dibujaban las siluetas del modelo a la escala deseada y se recortaban perfiles que, al sumarse, componían la escultura en tres dimensiones. En 1892, Joseph Blanther patentó, en los Estados Unidos, un sistema de creación de mapas topográficos en 3D utilizando un método de estratificación de principios similares a las impresoras actuales.2 Finalmente, en 1984, Charles Hall presentó la primera patente para una impresora 3D titulada “Aparato para la producción de objetos 3D mediante estereolitografía”, que fue la primera impresora 3D del mundo.3 El primer uso informado en Ortopedia fue en 1999 como una ayuda para la planificación preoperatoria de una cirugía espinal compleja.4
Para utilizar la impresora 3D, en primer lugar, se requiere de una tomografía computarizada de alta resolución de la deformidad, fractura o defecto. El programa de diseño asistido por computadora crea una representación digitalizada de un objeto que luego se convierte en un archivo de estereolitografía (STL). Los archivos STL “recortan” el modelo digitalizado creado por el programa de diseño asistido por computadora, lo que permite que la impresora 3D imprima el objeto capa por capa. Los materiales de impresión 3D más utilizados son titanio, acrilonitrilo butadieno estireno y ácido poliláctico.
Se describen tres tipos de impresiones:
1. La estereolitografía: primer método que se creó. Se aplica luz ultravioleta a una cubeta que contiene resina. La luz es controlada por una computadora y polimeriza la superficie de la resina en la cubeta dando forma al objeto. Por medio de un pistón que desciende, se va exponiendo más resina a la luz y se van creando las distintas capas sucesivas.
2. La sinterización selectiva por láser: fabrica objetos mediante el prensado de polvos u otras materias que previamente han sido calentadas sin llegar a la fusión. También se aplica una luz ultravioleta, pero, en este caso, actúa sobre un polvo, en lugar de hacerlo sobre resina líquida. Se produce una adición por capas solidificando el material.
3. El modelado por deposición fundida: en este caso, el material utilizado es un filamento de plástico que pasa por una resistencia en una boquilla que lo calienta por encima de los 200 °C y lo funde para depositarlo sobre una plataforma móvil. Esta tecnología es más sencilla y accesible.
Alin L. Garay, Micaela Cinalli, Lara Fernández, Fermín Inchaurregui, Julia A. Ruesta Alava, Agustín Arrieta, Pedro L. Bazán
Servicio de Ortopedia y Traumatología, Hospital Interzonal General de Agudos “General José de San Martín”, Buenos Aires, Argentina
Para descargar la investigación completa haga clik a continuación:
https://raaot.org.ar/index.php/AAOTMAG/article/view/1839/5656